Ti Koï is a Menorquin 55 which sails mainly between the Camargue and the Bassin de Thau. During a refit, her owner Jean Hersen noticed some blisters in the gelcoat of the hull. Once pierced, these blisters let out a liquid with a strong smell of vinegar, characteristic of osmosis. The MEF shipyard in Frontignan (Hérault) was chosen for the work on the boat.
Putting the boat ashore
The boat is pulled ashore. The entire hull must be planed to remove the old layers of antifouling and especially the porous gelcoat. To allow the tools to work without hindrance, the 2 propellers are removed as well as the through-hulls located under the waterline.
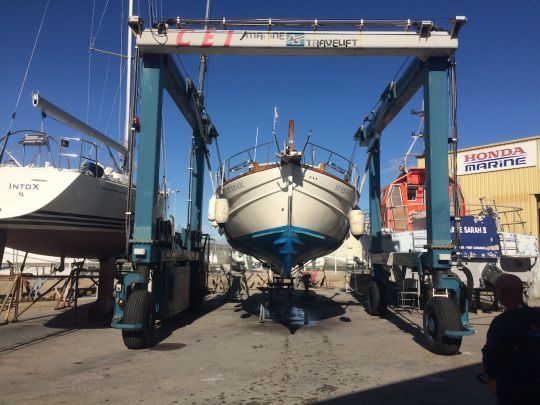
Peeling of the hull
The job site employs a power planer set to remove the old surface layers until the fiber is exposed. It is a delicate operation that requires a good eye and a steady hand, otherwise it can cause "steps" that would be tedious to take again. It is a tedious, noisy, dirty job... A well-equipped professional will usually complete it within a day.
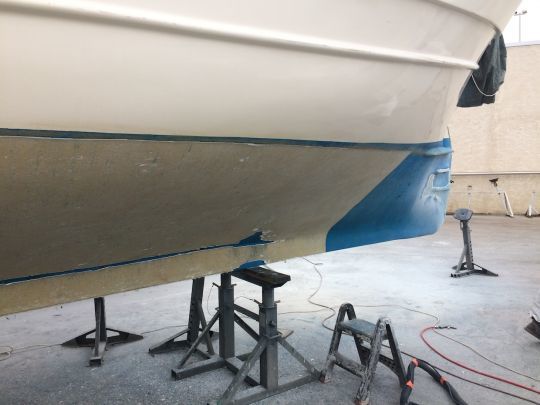
A captivating smell
Once the polyester is exposed to the air, the acidic solution that was trapped behind the gelcoat gives off a strong vinegar smell. This liquid is mainly composed of acetic acid that has concentrated in the polyester fibers. It is imperative to passivate this acid by dilution and to eliminate it by rinsing.
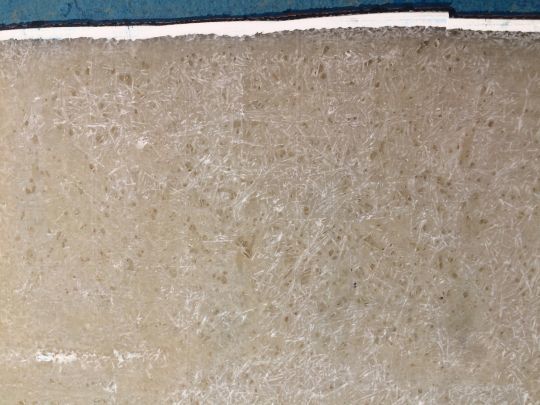
Water drying...
A first rinse is done with a high pressure cleaner as soon as the planing is finished. The polyester must dry thoroughly and, as surprising as it may seem, this drying is facilitated by regular rinsing of the acid that rises to the surface of the material. These rinses are done weekly at first, but can be spaced out as the PH of the polyester approaches neutral.
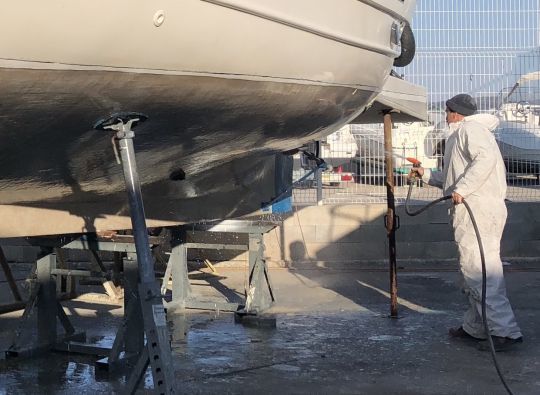
Percentage of humidity
The moisture content of the polyester is regularly measured with a tester. This control is done at various points of the hull, at locations marked so that the measurements are comparable from one time to another. This monitoring ensures that the drying process is progressing well and that it is homogeneous at all points of the hull.
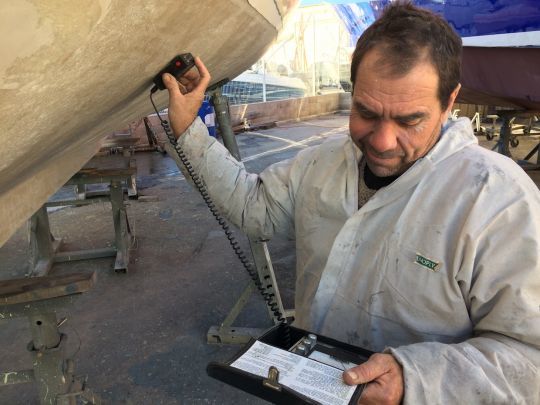
Treatment also of the interior of the boat
To avoid condensation from the inside, the bilges are emptied as well as the tanks molded in the hull. Also to facilitate drying, all fittings and access hatches to the bilges are kept open to ensure the best possible ventilation.
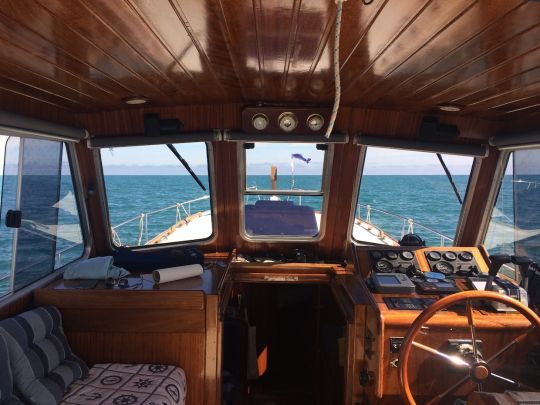
To all winds!
The drying phase can last from 6 to 12 months depending on the condition of the boat and the weather conditions. For Ti Koï, 9 months will be necessary, a time used by Jean Hersen and his wife to renovate the interior woodwork of the boat .
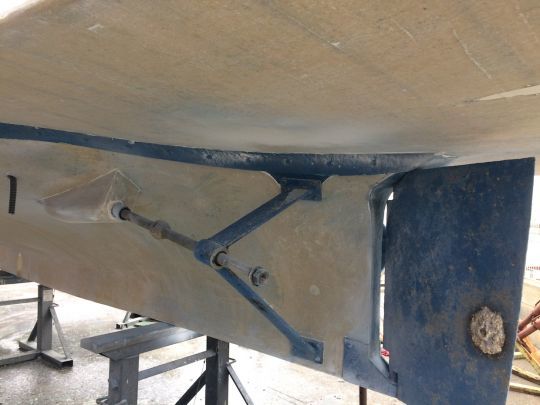
Brush and roller application
The treatment begins with the application of an epoxy primer with a roller and a brush to fill in every crevice of the polyester. The goal is to provide the best possible protective barrier and adhesion for the rest of the treatment, in this case a Gelshield International.
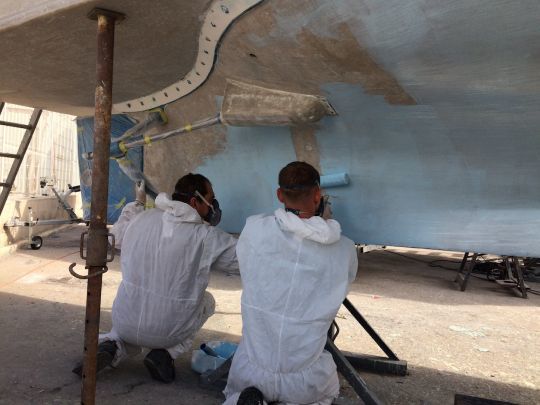
The shape and the line!
In addition to its protective function, the primer allows better visualization of surface defects caused by planing. The art of the job is to "re-shape" the hull, i.e. to give it back its shape, lines and surface aspect as perfect as when it came out of the mold. An epoxy coating is used, which can be applied in thick layers, dries quickly and is easy to sand.
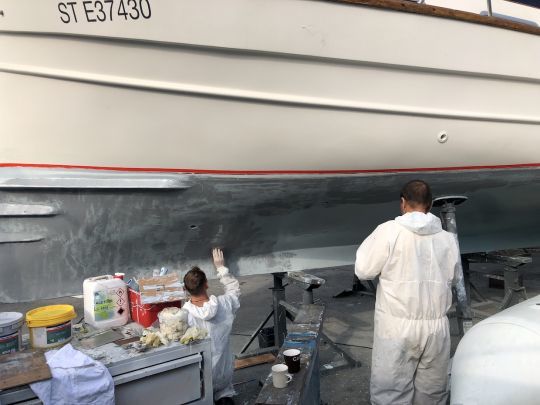
The joys of sanding!
A first sanding allows to reconstitute the lines of the hull. It is at this stage that the workers appreciate the quality of the planer's work and pester the architect who has placed so many indentations and strakes on the hull! The defects of aspect are puttied and sanded and several layers of primer are applied. Sanding is greatly facilitated by the colors of the coats which are visual markers.
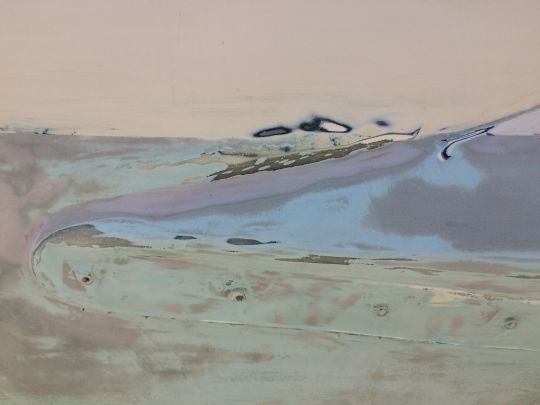
Last layers of surface !
An epoxy primer called "before antifouling" is applied. The recommended drying period is 10 days, which is used to install new hull fittings, new anodes and put the propellers back in place. At the same time, a veil of paint is applied to the bottom of the planks to make up for the parts affected by the planing at the waterline.
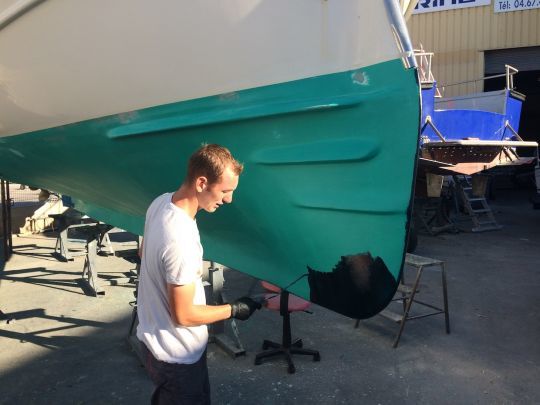
Like new!
After 2 coats of antifouling and nearly 10 months in the dry, the boat was put back in the water. She has never looked so good and Jean Hersen was able to take advantage of this time to work on her boat with the help of the yard's expert advice and facilities. Of course, the bill is high, close to 15,500 Euros including tax, but it is the price of a professional intervention.
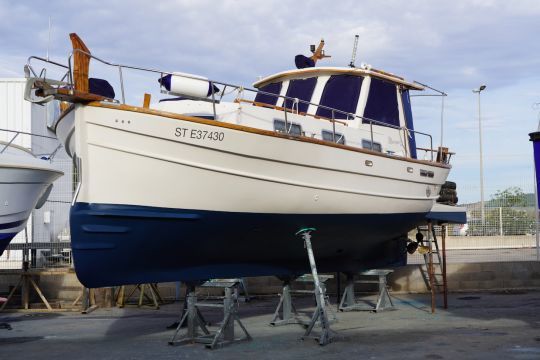