Precise tooling to save weight and stiffness
The construction of the Dehler 30 OD aims to obtain a sailboat that is both very rigid, to avoid deformations under load, and to respect a light weight specification in order to be efficient in light airs and downwind.
We know that mass industrial production is not very compatible with performance requirements, which is why the German manufacturer has adopted a sophisticated manufacturing method that is similar to semi-crafted sites.
First of all, the mould is shaped with extreme precision thanks to their tooling, in this case a 5-axis digital milling machine. It is a huge block of polystyrene that will be sculpted by a rotary cutter. From this block, the preforms of the hull, deck and internal structures will come out, which will respect the architect's plans to the millimetre.
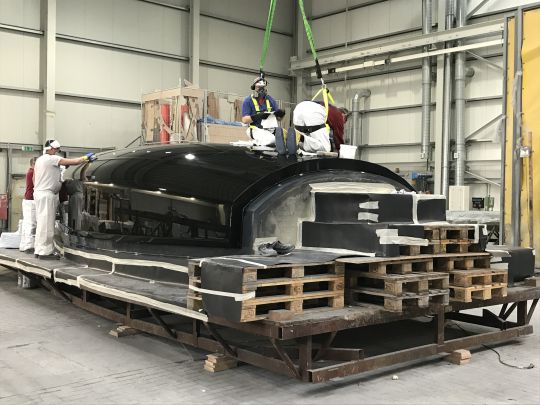
It is on these preforms that the composite moulds will be manufactured, from which many identical copies will be produced.
The accuracy of these tools is crucial. Dehler wants to innovate in its construction methods by assembling all the structural parts in the hull still held in its mould. It is a guarantee of rigidity allowing you to face heavy weather and to use the sailboat during the race. The respect of the dimensions is essential if you do not want to fill the gaps with a high thickness of glue.
The multiplication of the inserts avoids the use of a global counter mould as is often the case. This choice is much lighter, but it is also much more complex and expensive in terms of production hours.
A quality implementation and choice of materials
An efficient racing boat is not necessarily all carbon. The Class40s are proof of this, to such an extent that they often compete with older generation Imoca, even though they are built like all-carbon goldsmiths' pieces.
Thus, the Dehler yard opted for a production process similar to the Class40s, namely a fibreglass sandwich composite, an infused vinylester resin, and a PVC foam sandwich core.
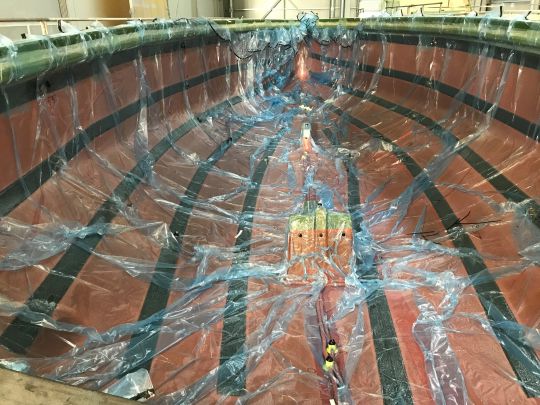
Few construction sites push this manufacturing process to each partition, to structural parts and to the slightest cover. In addition, some monolithic elements such as the screens are reinforced with carbon to ensure optimal lightness and avoid excessive glass fibre thicknesses.
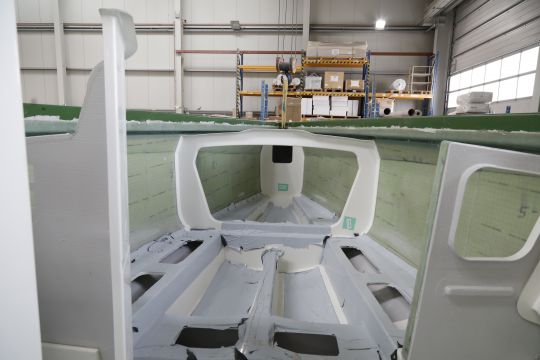
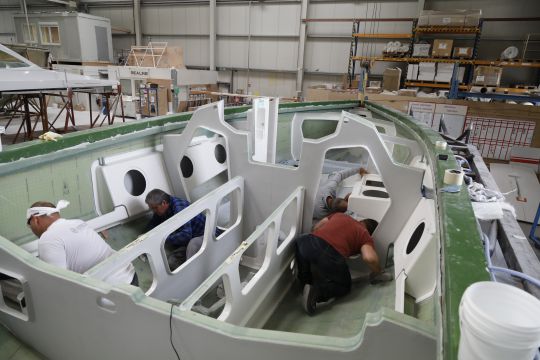
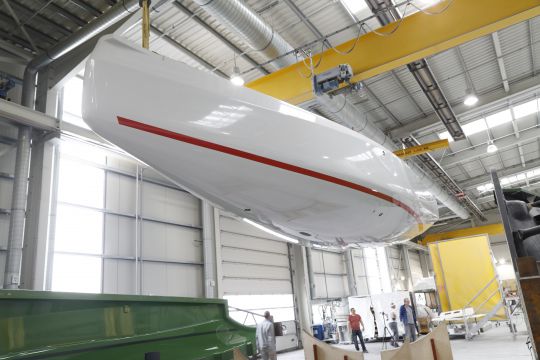
A composite keel to lower the centre of gravity
The ambition of lightness is accompanied by an objective of lowering the centre of gravity. This work is a long addition of optimizations from the masthead to the keel bulb. And precisely, the yard opted for the manufacture of a profiled composite keel sail with a torpedo-shaped lead ballast.
This construction method, combined with the 2.20 m draught, ensures a very low centre of gravity for this appendix. This choice, compared to a cast iron or all-lead keel, reduces the overall weight of the keel while maintaining a high righting torque. It could not be more optimized.
Again, this technical approach is not very visible and costly, but it is most effective in achieving performance objectives once on the water.
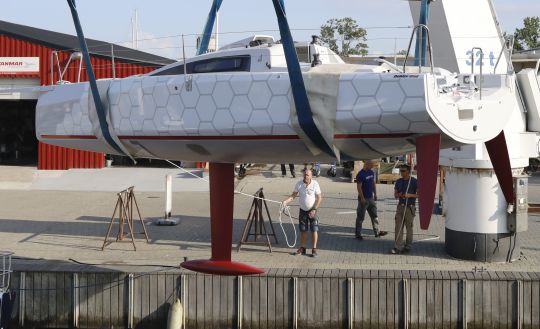
The virtuous circle of lightness
If the boat is light, the rigging will receive less effort. However, this does not mean that optimization at the bridge level should be stopped. In order to reduce the weight in the heights, which are so harmful to the stiffness of the canvas, the mast is made of carbon, which ensures great lightness.
Indeed, to facilitate the use of a mainsail with horn, Dehler has opted for very push-up spreaders. The angulation of the spreaders induces significant compression in the mast. An aluminium spar would be too thick and therefore too heavy to support this compression.
Finally, the carbon mast - and its fibre draping, which can be optimised over its entire height according to the constraints - allows a single spreader spreader stage to be installed. This further reduces the weight and lowers the centre of gravity of the entire standing rigging.
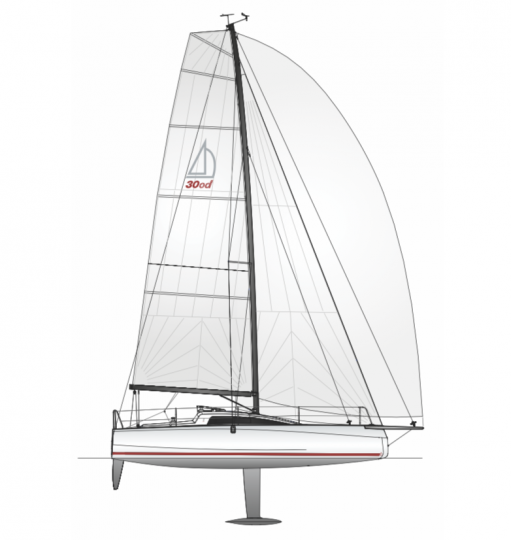