Specialist in epoxy resin
Sicomin is a French SME with 60 employees located mainly in Châteauneuf-les-Martigues (13). Its core business is the manufacture of epoxy resin, one of the three main resins, along with polyester and vinylester, used in nautical, pleasure (sailing and motor) and professional construction.
"Epoxy has better mechanical and thermomechanical values (temperature resistance). It is used for the manufacture of rather high-end pleasure boats or on racing boats. The resin is used for the assembly of all parts: lamination on decks, hulls, bulkheads. We use it in the manufacturing of the boat, but also for bonding."
In addition to resin production, Sicomin also offers core materials (foam, cork, etc.) and reinforcing materials (fiberglass, carbon, etc.) to complement the epoxy service.
A range of biosourced resin
"Sicomin is 35 years old and started working on biosourced resin about 15 years ago. The biosourcing work is only on the resin and not on the hardener. As a reminder, the polymerization of the material is done by mixing a resin and a hardener. We have developed the Greenpoxy family whose epichlorohydrin molecule is obtained from glycerol, a vegetable raw material. We use molecular mimicry by replacing a molecule derived from petrochemicals with a molecule derived from plants, a more noble raw material."
Today, the manufacturer has developed 3 biosourced resins. Greenpoxy 56 is the one that offers the highest rate of biosourced raw material with 56% of carbon of vegetable origin. To differentiate a petrochemical resin from a biosourced resin, a carbon 14 dating is performed. This will allow to validate the age of the molecule. If it is very high, then it is carbon, if it is recent, it is vegetable.
"Fifteen years ago, when we started working on R&D for a biobased resin and the supply chain for raw materials, it was not viable. We did not have access to sufficient quantities compared to the costs of these materials. For the past 5 years, the craze has been growing. There is a general awareness and the end customer is more and more vigilant. The consumer is more and more concerned about his environment."
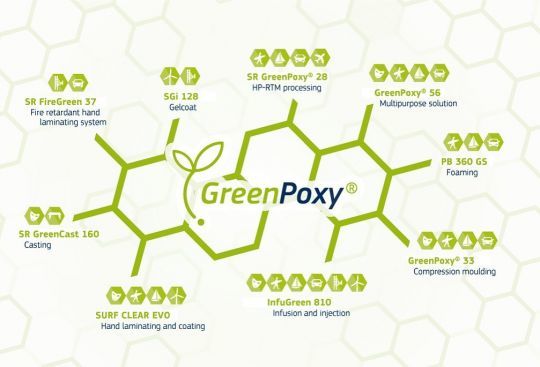
Application techniques similar to traditional resin
to date, biobased resins require the same manufacturing processes as carbon-based resins and offer the same mechanical resistance.
"When we decided to develop a biobased resin, we reformulated the base with biobased materials. Petrochemical resins and biobased resins are used with the same hardener. It's technically simple to switch from one resin to the other."
The price is also quite similar to a conventional resin. If the biosourced resin allows to minimize the environmental impact upstream of the construction, it is not recyclable afterwards.
"Epoxy resin is called thermosetting. It cures with heat and once cured, it is not recyclable. There are ways to recycle it, but they are very expensive and harmful in terms of pollution. It is not interesting to depolymerize epoxy. In this sense, we are working on the quality of our resins to offer a longer life."
Towards a 100% biosourced resin?
"All the developments that are being done tend to use as much plant-based feedstock as possible. Solutions are being developed in the lab, but not all the brakes are unlocked."
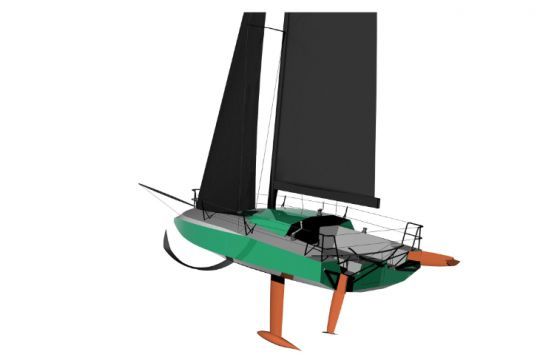
A global support in the choice of biocomposite materials
In addition to resin, Sicomin supports its customers in a more global way by offering them a range of more virtuous materials: natural fibers such as flax, which offers good results, coupled with epoxy fiber, hemp or basalt, core materials such as cork, PET foam (from recycled plastic) or balsa.
"Balsa is derived from wood. It was widely used in the 70's and 80's to make contact parts. But it was very sensitive to humidity and would rot if it got wet. Thanks to infusion, balsa is becoming interesting again, because it is a biosourced product with mechanical properties. At the same density, it outperforms all foams. Once infused, it is perfectly encapsulated and waterproof."
Developments for the future
Several developments are underway at Sicomin, starting with a high-modulus biosourced resin (high mechanical strength) for infusion or contact lamination construction. The SME is also working on a biosourced resin for wood.
"Epoxy is used for infusion, bonding, impregnation. For each of these processes, we make biobased epoxies." concludes Laurent Lacoste.