The mould, a key element in the construction of a composite boat
Each material has its own characteristics. If the mechanical strength or weight of the material used plays an essential role in the robustness and behaviour of the future boat, its plasticity and its forming capacity (possibility of making it take the desired curves) are determining factors in the way the boat is built. Boats made of wood, steel or aluminium can easily be manufactured without a mould. The structure of the future unit serves as a support on which the builder will fix the planks (the outer skin) of the hull. The main constraint is the limitation of possible hull shapes due to the relative rigidity of the wooden planks or metal sheets.
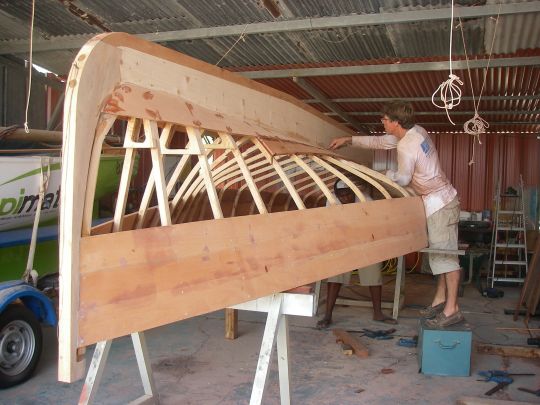
The advent of composites in yachting and their flexibility has allowed an almost absolute freedom of form. On the other hand, the mould has become an essential tool. A support is essential to give the fibreglass fabric its shape before impregnating it with resin.
Male or female mussel?
There are 2 main families of moulds for composite parts:
- male molds, whose shapes are "protruding"..
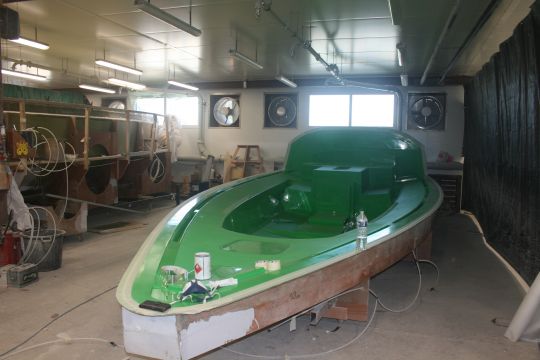
- the female mussels, whose shapes are "hollowed out"..
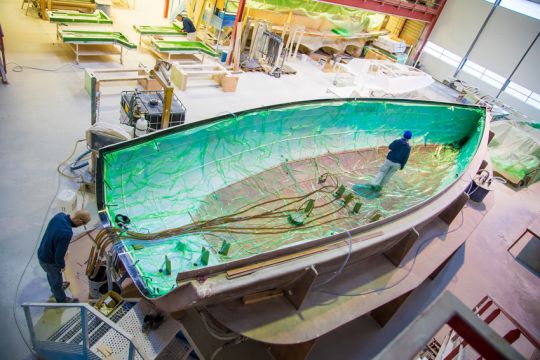
The moulding of parts in yachting is most often done in open moulds. Only one surface of the final part is in contact with the mould. For some processes, a closed system integrating a mould and a counter-mould is used, as explained in the diagram below.
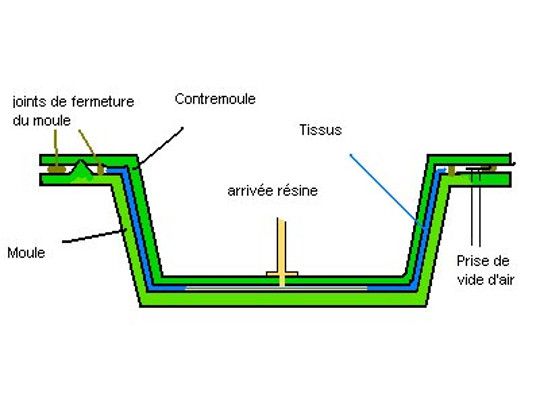
The choice of the type of mould is guided by several criteria, both technical and economical. In the case of open mould construction, the most common in yachting, the first criterion is the side for which the finish is the most important. Indeed, the gelcoat that guarantees the quality of the surface finish is applied to the mould. For a hull, where the outside face is the most crucial, the female mould is preferred. For a deck, the male mould ensures that the upper surface has the right finish.
However, the production cost of the mould is also taken into account, depending on the expected number of pieces. In the case of series production, the eligible investment is higher, as the number of boats produced guarantees depreciation. For our mystery photo, this is a unitary construction. The construction of a wooden mould, coated, proves to be more economical, in spite of the additional finishing time it will take to coat the outside of the hull and obtain a smooth hull.
Mould making process
The mould of our mystery photo is built in several stages:
- Installation of plywood or medium sections
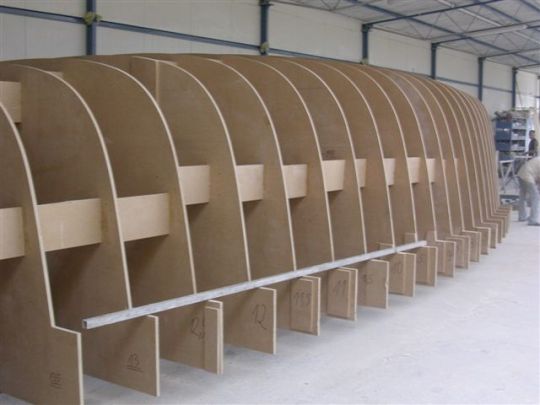
- Installation of healds
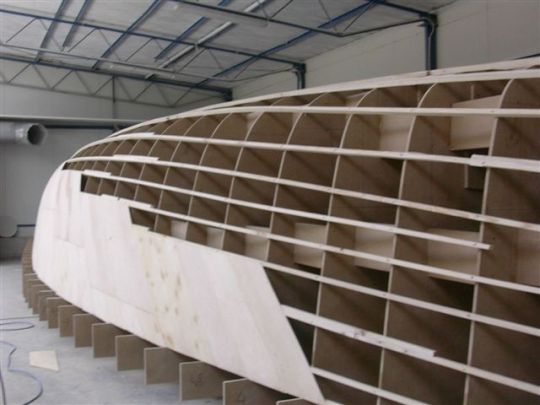
- Veneering of fine plywood surfaces
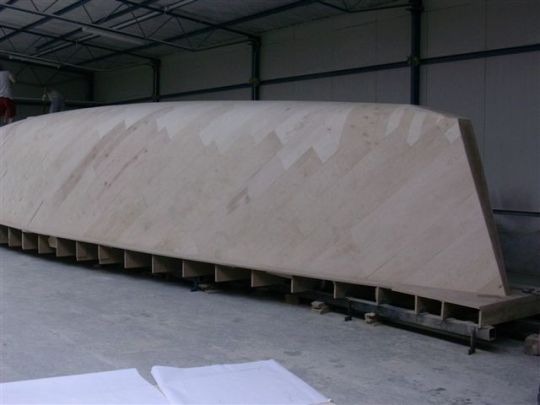
- Coating and recoating of surfaces up to a "mirror polished" finish level
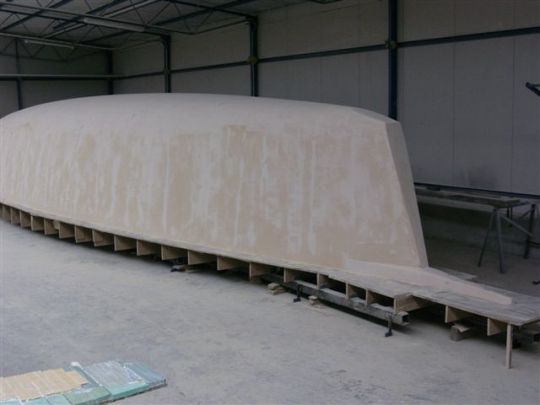
The geometry of the hull is obtained. Now all that remains is to begin the construction of the hull, but that's another matter !