This is 1995. At that time, more than 25 years ago, the first sailboats built in infusion were the J/110, a manufacturing process under a license called "Scrimp Process" which has since fallen into the public domain. Historically, J Composites was the first shipyard in Europe to build a sailboat in infusion. This is a good illustration of the lead and expertise taken by the shipyard in this process.
The expertise of this construction technique allows a perfect mastery of all aspects of the infusion. Today, the structural parts that make up a J Composites (hull, deck, bulkheads...) are all made by infusion.
For many shipyards that also use this technique, this choice was imposed in order to meet European styrene gas emanation standards and to respect working conditions for employees. Industrial and environmental reasons. At J Composites, this choice is above all a technical choice used only for the mechanical characteristics offered by parts built in infusion.
What's herbal tea?
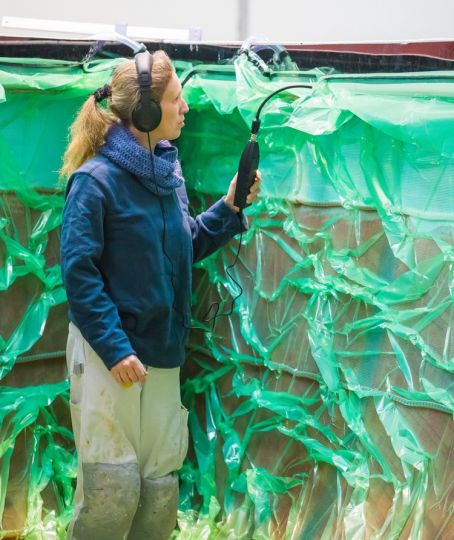
This involves placing all the elements that make up the part in the mould and then covering them with a waterproof tarpaulin. By sucking with a pump, a vacuum is created that seals each layer. Resin is then allowed to penetrate through pipes (diffusion line). When the vacuum is applied, the resin is evenly distributed throughout the fabric.
Why herbal tea?
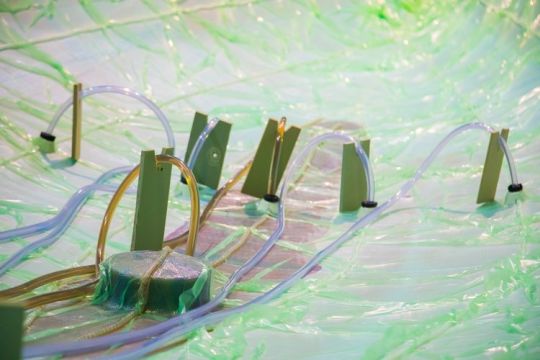
Building in infusion allows a perfect cohesion of the parts by compacting the fabrics perfectly. In addition, we are sure to obtain a good resin impregnation of all the fabrics. Above all, the weight of the finished part is perfectly controlled by injecting a very precise quantity of resin, no more and no less.
When talking about good impregnation, it is good to specify what a good % impregnation is. This can be illustrated by comparing the different solutions:
- Industrial laminate = 30% fiber + 70% resin
- Carefully hand laminated = 40% fibre + 60% resin
- Infusion = 60% fiber + 40% resin
Considering that the resin just serves as a glue to allow the fibre to develop its mechanical characteristics. Enough of it is needed, but putting too much of it only adds extra weight without improving the mechanical characteristics.
In the end, the infused piece is stiffer and lighter than the same hand layered piece. For a sailboat, stiffness and lightness rhyme with performance..
Why the sandwich?
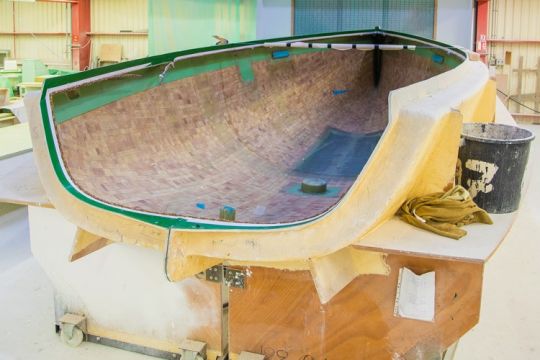
J Composite uses sandwiches rather than monolithic materials to build its boats. In fact, the same piece with the same resistance weighs 1.5 to 2 times more than the same piece in sandwich. In addition, a sandwich part is much stiffer than its monolithic counterpart.
What material for the core of the sandwich?
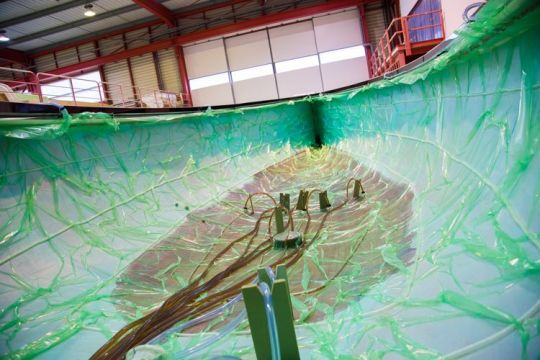
J Composites uses 2 types of core: foam and wood (balsa). The choice is mainly dictated by the very rounded hull shapes of the J Boats. Indeed on flat surfaces, not very developed, a foam core can be used. But on the curves, balsa (especially the Extra Light used at the yard), even if it is a little heavier than foam, fits better and limits the amount of resin used. In the end, the sandwich is lighter than if it was made entirely of foam.
In addition, balsa wood is more resistant to compression and impact. Thus the hull bottoms (the lively works) on which the waves hit, are all made with a balsa sandwich. The planks, flatter surfaces are made of foam.
To adjust the core in the mould, J Composite uses manual preparers. They are in charge of adjusting the different panels as closely as possible to avoid gaps between them. In fact, the resin is installed in these hollows. But the resin is heavier than the core. This increases the weight of the hull without making it stronger. This manual adjustment work ensures a perfect quality of the sandwich. An industrial approach with digital cutting for a quick installation by a preparer does not have the precision of a longer and more meticulous manual installation.
Infusion how does it work?
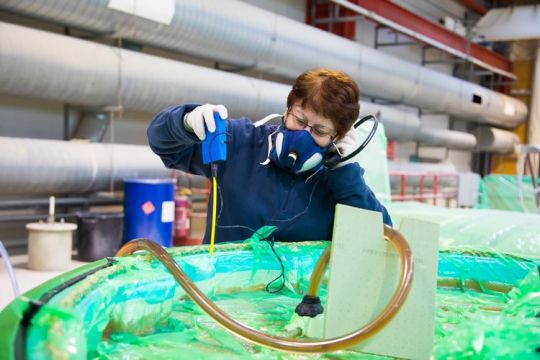
To be well infused, a strict process must be followed to the letter. Once the hull is ready, covered with a tarpaulin, an operator turns on the vacuum pump. This creates a vacuum at -1013 hPa. He then tries to detect any air leaks with a vacuum detector. There is then still time to plug them. During the entire infusion period (approximately 1 hour for D 112), he will carry out a visual check of the proper circulation of the resin. The diffusion lines (5 on each side) are opened successively from the bottom of the hull, gradually going up the planks.
The temperature must be perfectly controlled throughout this phase. This is what ensures the fluidity and setting of the resin. Indeed, if it is too hot, the resin will be too fluid and will catalyse too quickly, whereas if it is too cold, the resin that is too thick will not diffuse well.
After this hour of infusion, the vacuum pump continues to run to ensure the vacuum is maintained and the fabrics are well compacted throughout the drying time of the resin. It is also a guarantee of quality construction.