Trials in boat building
To race the Route du Rhum 2022, Roland Jourdain has built a 60-foot Ultramarine 5X made of at least 50% linen fiber .
"Flax fiber has many advantages. It is produced in a short circuit, has properties close to those of fiberglass and is much less energy consuming to produce." summarizes Roland Jourdain. The largest piece ever made of linen is the deck of the 18 m long and 9 m wide catamaran.
After tests on surfboards, paddles, or small boats, flax is now used on larger units. The Breton shipyard IDB Marine has manufactured two models from this material, a 9 m Virgin Mojito and another of its 6.50 m scow.
"Two years ago, we worked with IDB Marine to develop one of their linen models. The fiberglass was replaced by linen fiber. We accompanied them in the selection of raw materials, the design of the yarn and the fabric, in partnership with Kaïros. This was the first example in the yachting industry of series production, which comes from the desire of a customer to have an eco-responsible, local and sustainable boat. The technical aspect has also been respected with the standards sought on this type of boat. We are convinced that we can achieve the same technical resistance as fiberglass for yachting projects explains Laurent Cazenave, head of communications at Terre de Lin.
Positive feedback for mass production
"The material works well and it's really different in terms of the dust. The fibers are natural and when you grind, it's not allergenic." however, there is a slight difference in weight of 150 kg more (+6%) compared to the polyester model and a total price that is 3% higher, a fairly small difference. IDB Marine also offers the biocomposite construction of these models as an option.
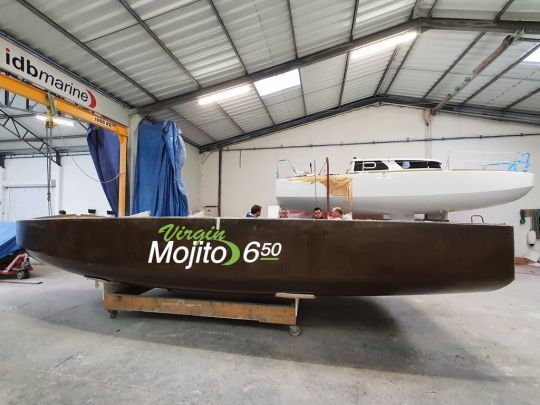
Terre de Lin, leader in the production of flax fibre
Terre de Lin is the most important agricultural cooperative for the cultivation and transformation of flax in Europe, if not the world. The largest concentration of linen production is located between Caen and Amsterdam and covers 90% of the world market for textiles. Based in Seine-Maritime, it supplies the linen that nautical companies use in the construction of their boats.
Specialized in textiles, it has invested for several years in R&D for the composite. Ten years ago, TDLT (Terre de Lin Technique) created a linen and carbon fiber reinforcement for Salomon skis. Over the past 5 years, several industrial successes have enabled the company to make a name for itself in the composite world. Even if the volumes are still modest compared to textiles.
An ideal fiber to replace fiberglass
"Flax fiber integrates well into the composite. It has a relatively light density, good vibration management and resistance to impact, shear and fatigue. It ensures the durability of materials over time. It has a real eco-responsible asset unlike fiberglass or carbon, and has mechanical characteristics close to those of fiberglass, apart from an interesting aesthetic aspect. All these advantages have aroused the interest of the composite industry. Another advantage is that flax can be integrated into conventional composite processing techniques. This was a necessary key for the composite players to be able to keep their traditional method." says Laurent Cazenave.
However, it was also necessary to reassure them for many years about the quality aspect of this material, as the communication manager explains to us.
"Flax is natural, so there is a vintage phenomenon. But the quality standard does not move and the quantity is always sufficient. We regularly supply the composites market." continues the communication manager.
With the construction of the We Explore bridge, it is another step forward for flax fiber construction.
" We Explore is a very strong eco-responsible approach. It is a large-scale piece, the largest piece ever made of linen fiber for this 60-foot catamaran. It is an additional technological challenge and a large-scale demonstration of the capacity of linen to integrate this type of project. The most important thing for us is to integrate the flax fiber in the project from the beginning. It is more difficult to replace a fiberglass part with a flax part. We are confident about the future of this fiber in boat building, concludes Laurent Cazenave.
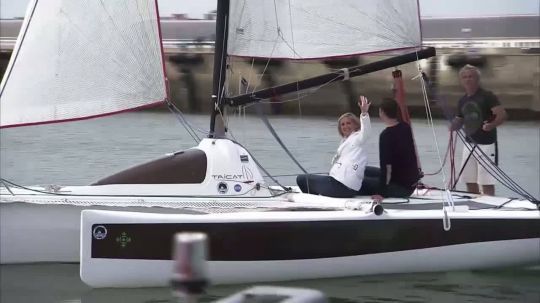
Flax, the future of boat building?
So is flax the future material for yacht construction?
"That's the goal, but we need to know what the time frame is." explains Xavier Desmaret, head of the Outremer site.
"We Explore is an experimental platform. With Roland, it will be tested in demanding conditions, often harder than what a yachtsman might encounter. So we're going to get some interesting feedback on how the material ages, but we're not going to put the cart before the horse. What is certain is that if we manage to do it on our boats, applications on smaller boats will be possible. If it works for us, it will work for many people, concludes the director of Outremer.